外循环流化床蒸汽锅炉产品特点
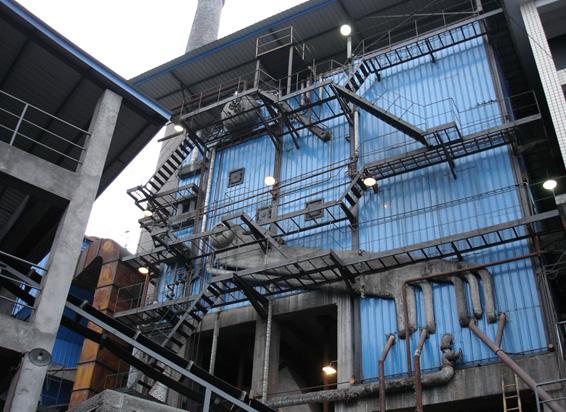
技术介绍
SHX型外循环硫化床锅炉产品特点
1、循环流化床锅炉因增加了飞灰分离及回收装置,达到了燃料的循环燃烧,具有以下诸多显著特点:
① 燃烧效率高
一般燃料效率可达97~99%,净含碳量小于2%,锅炉运行热效率大于85%;
② 煤种适应性广
不仅各种烟煤均可稳定高效燃烧,甚至链条炉渣、造气炉渣、煤矸石也可掺烧,可满足不同地域、不同用户的要求;
③ 负荷调节性能好
a、负荷调节比可达1:3,即在30%额定负荷下锅炉仍能高效稳定燃烧,这是链条炉、煤粉炉不能比拟的;
b、负荷调节速率快,最快可达10%,适合负荷多变的用户;
④ 洁净燃烧
有害气体排量低,因CFB炉为低温燃烧(900℃),故NOX排量低,可控制在150ppm以下。加入石灰石,可使脱硫率控制在90%,而且费用低廉,粉尘排放采用静电、布袋或多级水膜除尘,可使排尘控制在国家现定标准之内;
⑤ 投资回报率高 因高效节能,与链条炉比,约0~2年即可回收锅炉投资,经济效率显著;
⑥ 灰渣综合利用 CFB锅炉为低温燃烧,炉渣活性好,呈片状结构,可直接用于制砖、硅酸盐水泥、熟料、火山灰粘结剂代用品等,提高了综合效率。
2、 采用成熟的高温旋风分离结构,分离效率高,保证锅炉可靠持续高效运行。采用高强耐热耐磨不锈钢旋风分离器中心筒,提高了寿命。
3、 采用可靠的电气控制系统,保证锅炉安全、正确运行,主要控制项目有:
① 料床炉温控制、报警及风机、给煤连锁;
② 高低水位控制、报警及水泵、风机、给煤连锁;
③ 超压保护、控制、报警及风机、给煤连锁;
要求高的用户还可配备计算机自动控制,达到负荷、压力、温度、水位及燃烧的自动控制,以正确协调,风机、水泵、给煤的细微调正,保证安全、正确、高效的燃烧及负荷供应。
TG型外循环流化床锅炉产品特点
1、锅筒:
筒身由20g钢板卷焊而成,封头是用同种钢板冲压而成。
锅筒内部装置由旋风分离器,顶部分离板,连续排污管,紧急放水管,给水管,加药管组成。旋风分离器直径为ф290,共14只。
由旋风分离器出来的蒸汽穿过上部波形板箱,再经锅筒顶部波形板分离器箱,然后由蒸汽引出管到引入到过热器系统。在锅筒顶部布置有波形板分离箱做为细分离,并在波形板分离器下装有4根疏水管,把分离箱中带进的水份再送回锅筒的水容积之中,以保证蒸汽器质。
锅筒上除布置必须的管座外,还布置了再循环管座,吹灰管座,紧急放水管座,备用管座。
为防止低温的给水与温度较高的锅筒筒壁直接接触,在管子与锅筒筒壁的连接处装有套管接头,给水进入锅筒之后,沿锅筒纵向均匀分布。
锅筒装有两只就地水位表,此外还装有两只电接点水位表,可把锅筒水位显示在操纵盘上并具有报警的功能。另外,锅筒上配有备用水位管座,用户可用于装设水位记录、水位冲量等仪表,可实现对水位的自动控制、自动记录。
为提高蒸汽的品质,降低炉水的含盐浓度,锅筒上装有连续排污管和炉内水处理用的加药管,排污率为2%。
锅筒通过锅筒支座支于钢架上,可沿轴向自由胀缩。
2、水冷系统
炉壁、炉顶均由膜式水冷壁组成,通过水冷上集箱上吊杆悬挂于炉顶钢架上。燃烧室上部与炉膛膜式水冷壁相接,下部与水冷风室及水冷布风板相接。水冷风室由膜式水冷壁钢管组成,内焊销钉以固定耐火材料,水冷布风板由ф60钢管及6×45扁钢组焊而成,在扁钢上开有小孔与风帽相接。
炉膛本体分成左、右、前、后四个水循环回路,引汽管由ф133×5钢管组成,由2根ф219×8钢管组成集中下降管。在每个集箱装有排污阀门以便定期排污。
为了降低返料温度,降低炉墙重量,缩短起炉时间,增加密封性及运行的可靠性,在旋风筒锥体部位设置了一个水冷旋风分离器。
水冷分离器有以下特点:
(1)耐火材料用量降低,从而使锅炉承重减轻,用户耐火材料费用减少。
(2)锅炉启动时间明显缩短。
水冷分离器由120根ф32×3.5管子和上下两个ф159环形集箱焊接而成,管子上焊有销钉以敷设高强浇注料,整个分离器由下集箱支撑向上膨胀,上集箱引出管与固定护板之间设有膨胀节以保证密封。
旋风分离器内衬采用耐磨、隔热材料。
在锅炉正常运行条件下,环境温度为27℃时,旋风分离器外表面温度不大于50℃,当环境温度大于27℃时,旋风分离器外表面温度允许比环境温度高25℃。
旋风分离器下端回料立管结构合理,确保分离效果,并避免噎塞或气流扰动影响分离效果。
旋风分离器上部烟气出口管即中心筒采用耐磨耐高温材料制造,出口管延长进入旋风分离器筒体一定长度以阻止烟气短路。
以上锅炉承压件材料均匀为20(GB3087-1999)无缝钢管。
3、过热器
本锅炉过热器分II级。
为保护旋风筒出口及尾部烟道顶部的炉墙,在此部位特别设有炉顶包敷管,包敷管下部焊有销钉,其上固定耐火浇筑料,饱和蒸汽从锅筒由连接管引入顶棚管进口集箱再进入炉顶包敷管,炉顶包敷管在尾部烟道上方作为悬吊管引入吊管出口集箱进入低温过热器加热后,分别进入两个喷水减温器减温。过热蒸汽减温后引入高温过热器进口集箱,经高温过热器管系加热后进入高过出口集箱,经主汽阀送往汽轮机。
低温过热器、高温过热器均由ф42的管子组成,且均采用顺列布置以降低磨损和积灰。每级过热器迎风第一排都设有防磨罩。过热器减温系统采用喷水减温。减温器置于两级过热器之间,这样既可保证汽轮机获得合乎要求的过热蒸汽,又能保证过热器管不致于因工作条件恶化而烧坏。
为保证安全运行和传热效率,低温过热器采用逆流布置,高温过热器采用顺流布置。低温过热器采用20(GB3087-1999)的无缝钢管,高温过热器采用15CrMoG(GB5310-1995)的低合金无缝钢管。
4、省煤器
本炉省煤器系螺旋鳍片管式省煤器,三级布置,为ф32×3的20(GB3087-1999)无缝钢管与19×1.9的鳍片组成,给水沿鳍片管自下而止,与烟气成逆向流动。
为减少磨损,省煤器系统采用顺列布置。
为保护省煤器,在锅筒与省煤器进口集箱之间设有再循环管,以保证锅炉启动过程省煤器管子的水能进行自然循环。
锅炉尾部烟道内布置的省煤器等受热面管组之间,留有足够高度的空间,供进入检修、清扫。
省煤器入口联箱设置牢靠的固定点,能承受主给水管道一定的热彭胀推力和力矩。
5、空气预热器
锅炉采用管式立式布置空气预热器。
空气预热器为两级,空气分别由一次风机和二次风机从上下两个入口送入预热器,上面入口为二次风空气预热器,下面入口为一次风空气预热器。两级空气预热器均用ф51×1.5的螺纹烟管制成。由于螺纹烟管能有效破坏烟气的层流特性,所以螺纹烟管不积灰、传热效率高。一、二次风预热温度均达到150℃。
空气预热器设置安装露点测量装置的予留位置。
空气预热器每级漏风系数保证第一年运行不超过0.03,长期运行不超过0.05。
空预器下部烟风接口距地面有足够的净空,供烟风道及除灰设备的布置。
6、燃烧系统
燃烧系统由燃烧室、炉膛、旋风分离器和返料装置组成。炉膛下部是密相料层,最低部是水冷布风板,布风板截面均匀布置了风帽。风帽系加厚菌状螺纹连接,采用特殊耐高温、耐磨铸钢材料精加工制成。
经过空气预热器加热后的一次风,由风室经过风帽均匀进入炉膛。燃煤和石灰石经设在炉前的2台给煤机将煤送入燃烧室。落煤口上方设置了播煤风。
二次风约占总空气量的45%,经喷咀进入炉膛,喷咀分上,下两层布置,以利燃烧和炉温的控制,整个燃烧是在较高流化风速下进行,炉温控制在800-900℃。含灰烟气在炉膛中间出口处(为防止烟气偏流)进入后部旋风分离器,被分离的细颗粒经返料器返回炉膛循环再燃,离开旋风分离器的烟气经过热器进入尾部烟道,随烟气排走的微细颗粒可由锅炉后部的除尘器收集。旋风分离器采用特殊成熟结构可保证分离效率≥99.5%。由于分离效率高,可保证炉膛内有足够的循环灰量,减少尾部烟气含灰量,有利于尾部受热面的防磨。
为保证返料器工作可靠,进入返料器风室的高压风引用空预器前一次风以保证返料器返料顺畅、降低循环灰在返料器内的再燃率。同时在分离器处布置水冷系统,以保证易粘结性煤不结焦,不堵灰。
返料器较小颗粒的炉灰可以从旋风分离器下的返料器的细灰管排出。
本炉为床下动态点火,在风室后侧布置点火器,点火油为0 #轻柴油,油压为1.96MPa。
- 上一个产品:DZS“长短汽包”型水煤浆锅炉产品特点
- 下一个产品:SZS型水煤浆锅炉产品特点